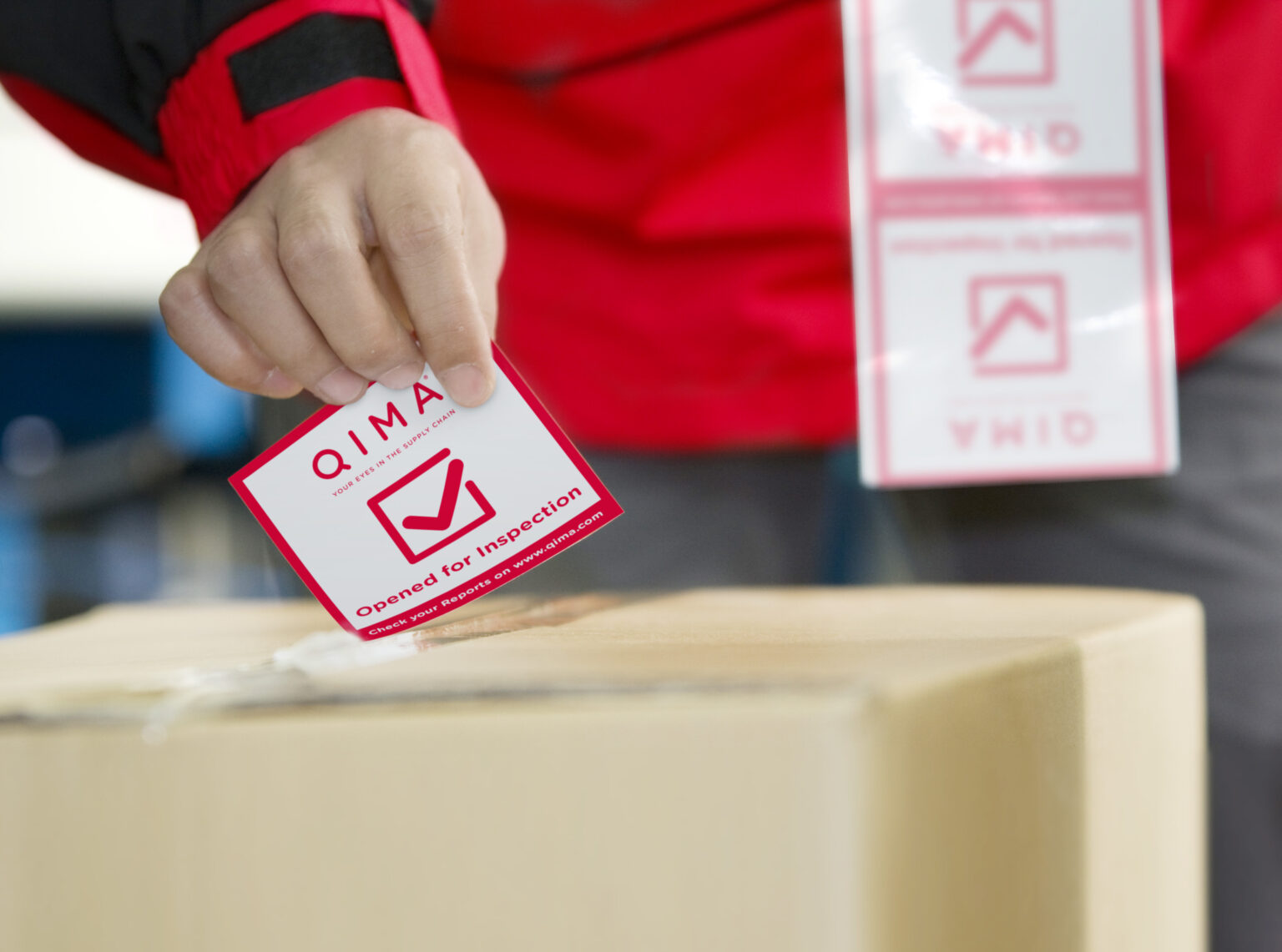
5 Critical Types of Quality Control Inspections
Introduction
Quality control inspections are an essential part of manufacturing, which are carried out to ensure that products meet the required standards and specifications. These include several processes that help in the reduction of waste and the prevention of defects during production. The services of a third-party inspection company like EC Global Inspection can help companies improve overall product quality.
Different methods are employed to maintain quality control through the stages of the production process. Understanding these various types of quality inspections will help companies looking to implement the best QC practices.
Here, we examine several critical types of quality control inspections that are often useful to manufacturers during production processes. These will help companies and brands maintain customer satisfaction and a reputation for quality. This article explores five critical types of quality control inspections.
5 Critical Types of Quality Control Inspections
Quality inspection is crucial for brands and companies to maintain a competitive edge in their respective markets. They involve processes such as the following:
Pre-production Inspection
Pre-production inspection is a quality control process where the material parts or components from the suppliers are thoroughly scrutinized. This is usually carried out to ensure that these meet quality standards and specifications that make them perfect for use during manufacturing. It is a vital process for factories or any company that relies heavily on the supply of raw materials or components.
When a pre-production inspection is carried out, the components undergo a visual examination used to detect defects and damage. Sometimes, the materials are measured to ensure they meet the standard dimensions. They can also be tested for required properties like strength and conductivity.
If the materials all meet the specifications, they are accepted for use in the manufacturing process. The results of the inspection will indicate what the next logical step should be. Materials that do not meet the required standards are rejected for corrective actions to be taken.
In-process Inspection
In-process inspection involves the examination of the products while they are still being manufactured. This is done to ensure that each is being made strictly according to the required quality standards. It is a process that can help with the early identification of any issues or defects so that corrective measures can be taken. Its frequency often depends on the complexity of the manufacturing process. This is because a product with strict safety requirements may need a more detailed in-process inspection than one with lower standards.
During an in-process inspection, each product and its components are carefully examined for inadequacies or any physical defects. After this, they are tested for qualities like durability and measured for adherence to dimensional requirements.
After it is done, it is easy to determine whether the production is being carried out according to the required quality standards. This way, the products are certified perfect for the next stage in the manufacturing process.
Final Inspection
This is a quality inspection of manufactured goods that takes place before they are released from the factory to the customer. It is necessary to ensure the products meet the specifications for quality before being shipped.
This process usually involves a visual inspection of each item for any type of damage to its parts. Its dimensions are measured to ensure adherence to physical requirement standards. After this, the products can be tested or information on qualities like safety, functionality, and reliability.
A final inspection is a crucial part of quality control for companies that manufacture, especially those whose products come with critical safety requirements. Any oversight in the strict stipulations tends to attract different types of liabilities. Each product is given a final inspection to reduce risk and avoid damage before it is released to the customer.
Statistical Process Control (SPC)
Statistical process control involves the use of statistical methods to observe and control the stages of manufacturing. Also known as SPC, it is carried out to ensure the stability of the production process for the consistent output of quality and standard goods.
During SPC, the process data is collected from the manufacturing stages using control charts that display its information. These are then analyzed over time to identify the variations or patterns that often lead to consistent problems with the products, such as physical defects and other issues.
Using the control charts makes it easier to determine if manufacturing is being handled correctly at the factories. It helps with getting information about the control limits of the production process based on the data collected. Processes within the control limits are stable enough to support the production of high-quality items for the duration of each major batch. The unstable ones can be eliminated or corrected to ensure better compliance with regulatory standards.
Product Testing
Product testing is a process that involves a test application of one of the manufactured items to verify its level of quality. The aim of carrying it out is to ensure that the products are safe and reliable for use as intended.
Product testing can involve a variety of tests, with the one to be used depending on the type of item and its intended use. This is why electrical devices tend to be tested for safety and performance features, while medical devices may undergo tests for usability, sterilization, and biocompatibility. Product testing can be conducted both during and after manufacturing, for a more timely observation of the process and its requirements. Asides from this, it also helps in identifying opportunities that can improve the products.
Conclusion
Quality control inspections are necessary to ensure that manufacturers can produce high-quality products according to the required standards of quality. Implementing them effectively helps companies interested in improving product quality and customer satisfaction. Asides from the five types mentioned here, there are others, such as AQL and PSI. To enjoy the best quality control services, contact EC Global Inspection. We have highly-trained agents across most factory locations who ensure all your quality and standard requirements are strictly adhered to.