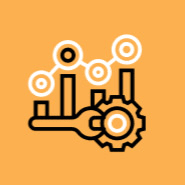
Design Optimization for Manufacturing: Enhancing Efficiency and Quality
Introduction:
Design Optimization For Manufacturing plays a crucial role in modern manufacturing processes, enabling companies to enhance their products’ efficiency, quality, and overall performance. By employing advanced techniques and tools, manufacturers can streamline production, reduce costs, and deliver products that meet or exceed customer expectations. This article explores the concept of design optimization for manufacturing and its significant benefits.
Understanding Design Optimization for Manufacturing:
Design optimization for manufacturing involves fine-tuning product designs to maximize their manufacturability and efficiency. It integrates various factors such as material selection, production processes, tooling, and assembly methods into the design phase. This holistic approach ensures that products are optimized for both functionality and ease of production, minimizing errors, rework, and production delays.
Benefits of Design Optimization:
- a) Enhanced Efficiency: By optimizing product designs, manufacturers can streamline production processes, minimize material waste, and reduce cycle times. Optimized designs lead to improved resource utilization, increased throughput, and enhanced overall efficiency.
- b) Cost Reduction: Design optimization helps identify cost-saving opportunities by eliminating unnecessary features, reducing material usage, and optimizing assembly processes. It enables manufacturers to produce high-quality products at a lower cost, enhancing their competitiveness in the market.
- c) Improved Product Quality: Optimal design ensures that products are manufactured consistently, meeting required specifications and quality standards. By addressing potential design flaws early on, manufacturers can prevent defects and quality issues, resulting in higher customer satisfaction.
- d) Faster Time-to-Market: Design optimization streamlines the production process by identifying potential bottlenecks and optimizing them in advance. By reducing the number of design iterations and minimizing rework, manufacturers can bring products to market faster, gaining a competitive advantage.
- e) Customization and Personalization: With design optimization, manufacturers can efficiently incorporate customization and personalization features into their products. By leveraging advanced manufacturing technologies, such as additive manufacturing and robotics, customized products can be produced cost-effectively, meeting individual customer preferences.
Techniques for Design Optimization:
- a) Computer-Aided Design (CAD): CAD software allows designers to create and modify 3D models, enabling them to visualize and optimize product designs before production. CAD tools provide features like finite element analysis (FEA) and computational fluid dynamics (CFD), aiding in optimizing structural integrity, performance, and manufacturability.
- b) Design for Manufacturing and Assembly (DFMA): DFMA principles help designers optimize products for ease of manufacturing and assembly. By considering factors like part consolidation, standardized components, and efficient assembly techniques, DFMA facilitates cost-effective production and improves overall product quality.
- c) Design for Six Sigma (DFSS): DFSS is a systematic approach that integrates design optimization with quality management methodologies. It enables manufacturers to achieve robust designs that meet customer expectations while minimizing defects and process variations.
- d) Topology Optimization: This technique uses algorithms to determine the optimal material distribution within a given design space. By removing excessive material and redistributing it where needed, topology optimization reduces weight, improves structural integrity, and enhances performance.
Case Study: Automotive Industry
The automotive industry exemplifies the benefits of design optimization for manufacturing. Manufacturers utilize computer-aided design tools to optimize vehicle structures, reduce weight, and improve fuel efficiency while maintaining safety standards. Advanced manufacturing techniques, such as 3D printing, allow the production of complex components with reduced weight and enhanced functionality.
Conclusion:
Design optimization for manufacturing is a critical process that empowers manufacturers to enhance efficiency, reduce costs, and improve product quality. By leveraging advanced tools and techniques, companies can streamline their production processes, eliminate design flaws, and bring innovative and high-quality products to market faster.