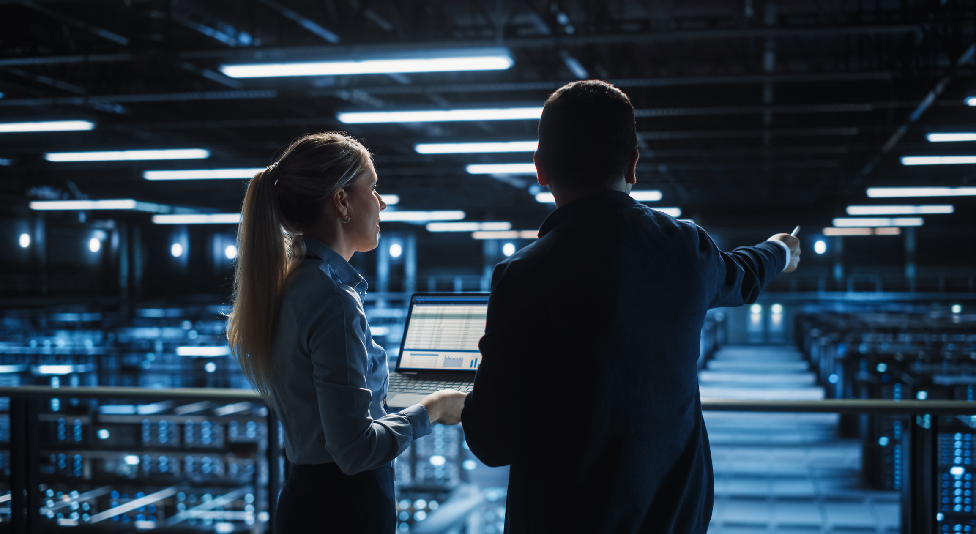
Securing Your CNC Machining Process: Cybersecurity and Sensor Technologies
In an era where digital technologies reign supreme, even traditional manufacturing processes like Computer Numerical Control (CNC) machining are not immune to the ever-present threat of cyberattacks. As CNC machining systems become more interconnected and reliant on digital interfaces, the importance of cybersecurity in this industry cannot be overstated. This article delves into the critical aspects of securing your CNC machining process, highlighting the role of cybersecurity measures and sensor technologies in safeguarding your operations.
The CNC Machining Revolution
CNC machining has revolutionized manufacturing by automating precision machining processes. These systems rely on computer-controlled equipment to shape and cut materials with unparalleled accuracy. While this automation offers incredible efficiency and precision, it also introduces new vulnerabilities.
Understanding CNC Machining Vulnerabilities
- Network Vulnerabilities: CNC machines are increasingly connected to networks for programming, monitoring, and data transfer. However, this connectivity exposes them to potential cyberattacks. Hackers can exploit network vulnerabilities to gain unauthorized access or disrupt operations.
- Data Theft: CNC machines store valuable design files, toolpaths, and production data. Unauthorized access can lead to data theft, intellectual property loss, and compromised designs.
- Production Interruption: Cyberattacks can disrupt CNC machining operations, causing downtime, missed deadlines, and financial losses.
- Quality Compromise: Tampering with CNC machining custom sensor components or code can result in subpar or defective products, which may have safety implications.
Cybersecurity Measures for CNC Machining
- Network Segmentation:
Implementing network segmentation isolates CNC machines from other systems, limiting the potential attack surface. This ensures that even if one part of the network is compromised, the CNC machining operations remain secure.
- Firewalls and Intrusion Detection Systems (IDS):
Robust firewalls and IDS solutions can prevent unauthorized access and detect suspicious activities in real-time, providing an additional layer of defense against cyber threats.
- Regular Software Updates and Patch Management:
Keeping CNC machine software, operating systems, and network equipment up to date is crucial. Manufacturers often release security patches to address known vulnerabilities.
- User Authentication and Access Control:
Implement strict user authentication mechanisms and role-based access control to ensure that only authorized personnel can access CNC machine controls and data.
- Employee Training:
Train your employees on cybersecurity best practices, including recognizing phishing attempts, using strong passwords, and reporting suspicious activities promptly.
Leveraging Sensor Technologies for Enhanced Security
Sensor technologies play a pivotal role in enhancing the cybersecurity of CNC machining processes. Here’s how:
- Anomaly Detection Sensors:
Anomaly detection sensors continuously monitor machine behavior and network traffic patterns. They can quickly identify deviations from the norm, signaling potential cyberattacks or operational issues.
- Environmental Sensors:
Monitoring the physical environment is crucial. Temperature, humidity, and vibration sensors can help prevent damage to CNC machines caused by adverse conditions, including cyberattacks that may attempt to manipulate machine parameters.
- Machine Health Sensors:
Sensors that track machine health can detect unusual wear and tear or deviations in performance that might indicate a cyberattack.
- Data Encryption Sensors:
To protect data in transit, employ encryption sensors to secure communication between CNC machines and other networked systems.
Conclusion
Securing your CNC machining process against cyber threats is paramount in today’s digital age. Implementing robust cybersecurity measures, such as network segmentation, firewalls, and employee training, is essential to safeguard your operations. Additionally, sensor technologies offer an extra layer of protection by monitoring machine behavior and environmental conditions. By combining these measures, manufacturers can ensure the integrity, security, and efficiency of their CNC machining processes in an increasingly connected world.